Guide to Career and Technology Studies (CTS)
Health and Safety Culture in the Workplace
Everyone in education, business, or industry is involved in promoting health and safety. The following are examples that reflect a culture of health and safety in the workplace.
Example: Off-Campus Preparation
Students who would like an off-campus placement must complete HCS3000 (Workplace Safety Systems). While not compulsory, the completion of a WHMIS course prior to being placed at a worksite is recommended and puts the student at a definite advantage with respect to personal health and safety. Off-campus education teachers/coordinators tour the business or facility in order to approve it for student placement, thereby deeming it a “safe” place.
A Worksite Registration Form provides teachers the opportunity to meet with the employer and discuss any health and safety-related aspects specific to that worksite that the student may routinely encounter.
A Student Learning Plan asks the employer if any of the following are offered: orientation, safety training, and certifications. In coordination with this documentation, a Workplace Hazard Awareness Assessment form also ensures that the student receives the necessary job-specific training and orientation to the required personal protective equipment for that worksite or job.
Throughout the placement, the Employer Evaluation of a Student Form is used to ensure students are evaluated on various health and safety skills. A positive attitude toward ensuring a culture of health and safety at the worksite that is respected and embraced by the students is a goal for any off-campus placement.
Example: Safety in Warehousing
In a warehouse environment, yellow caution lines are painted or taped on the floor to identify where equipment, such as a forklift, may be used. Caution lines keep workers out of the hazardous area and allow the forklift operator to work safely.
Example: Safety in Landscaping
Landscapers work with a large variety of tools and equipment depending upon the task or job. Employers provide landscape workers with the necessary personal protective equipment, such as hard hats, hearing protection, tinted safety goggles, suede work gloves, reflective vests, and steel-toed footwear (i.e., CSA-approved footwear that is worn above the ankle).
Example: Ladder Safety
If a ladder is used, signs are posted or a temporary barrier of orange cones or cording is used to ensure that other workers are aware that someone is working at a height in this area. Workers using ladders must not use the top two rungs, unless specified safe by the manufacturer of the ladder, as these two rungs present an unstable situation for the worker. Workers need to choose the appropriate height of ladder for the task.
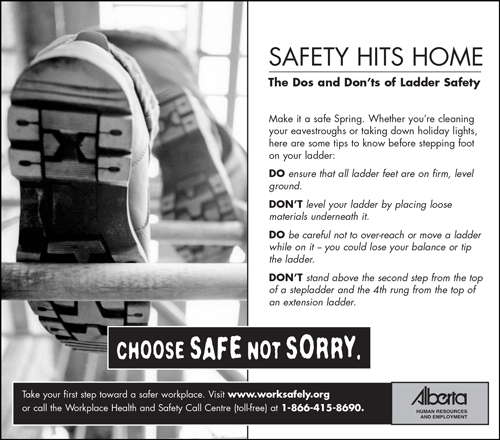
© 2011 Government of Alberta. Alberta Labour.
Work Safe Alberta http://work.alberta.ca/occupational-health-safety/ohs-posters.html
Example: Fall Protection
Occupational Health and Safety regulations state that anyone working at a height of 3 metres (10 feet) must wear fall protection. This means that workers doing a wide range of activities—washing windows, working construction, or pruning trees—must wear their gear to comply with the law and to keep them safe. An introduction to the safe use of fall protection is provided by the company and a fit-test is performed to ensure the worker knows how to properly and safely wear and use the gear. There are many types of fall protection available to workers.
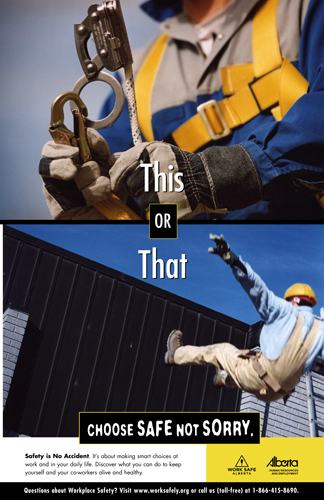
© 2011 Government of Alberta. Alberta Labour.
Work Safe Alberta http://work.alberta.ca/occupational-health-safety/ohs-posters.html
Example: Using Tag-Out for Tool and Equipment Safety
If a machine, a piece of equipment, or a tool is not working, businesses use a tag-out procedure. This procedure requires a tag to be placed at both the source of power and on the item itself that indicates there is a problem, locks the item, and prevents the item from being used. Once the source of power to the machine is disconnected, there is no possibility of a false start or someone inadvertently using the machine, equipment, or tool. In this way, the item is isolated and inoperable until it is serviced, repaired, or replaced. Everyone participates in this process to ensure that no one works with tools and equipment that are not in good working order.
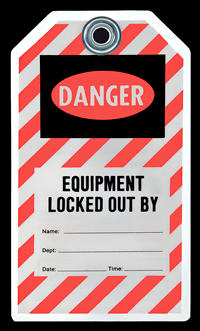
Hemera/Thinkstock
Example: IT Ergonomics
Preventing injuries due to improper chair height and computer screen height, incorrect use of the mouse, and inadequate lighting is addressed in IT work environments. As well, the repetitive nature of the job requires that the health and safety of the worker is considered.
Example: Personal Hygiene in the Food Industry
Good personal hygiene is practised in restaurant food-prep areas to ensure that food is handled properly and there is no cross-contamination with items that could cause illness.
Food is stored and prepared safely and properly according to guidelines set by the food industry.
Washing hands well before handling food is a priority.
Workers must wear hairnets to keep their hair from falling into the food that is being prepared.
Signs are posted around the kitchen to ensure awareness and compliance to laws and practices for safe food handling. These signs are posted so that all restaurant workers know the proper protocols for ensuring the personal safety of their co-workers and customers.
Example: Using Friction Strips and Caution Tape
Students working in a construction shop will see friction strips or traction strips placed in front of power equipment that has been bolted to the floor. Friction strips keep workers safe from slips, trips, or falls when operating the equipment. Yellow caution tape is placed around hazardous equipment to warn others of the danger and to give the person operating the equipment a safe place to work that is free from traffic. In the following picture, a safety zone is shown with traction strips inside.
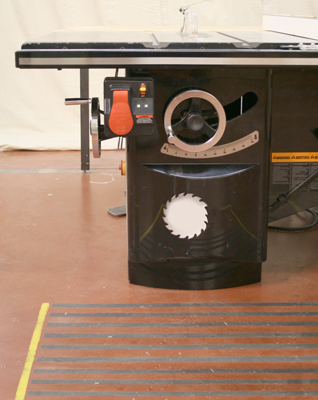
Example: Safety in the Health Industry
In the health industry, signs are posted to identify restricted areas; non-allergenic nitrile gloves are used in place of latex gloves; hand-wash stations are commonly placed near entrances and washrooms; and sharps containers are made available for safe needle disposal. Many procedures require that masks be worn to help prevent the spread of disease or sickness from airborne bacteria and viruses. Regular meetings provide opportunities for health professionals to get updates and discuss the latest protocols for ensuring personal health and safety.